Blogarticle
AutoBot - using robots for better battery cells
The first battery cells are to be manufactured in the Fraunhofer "FFB PreFab" as early as this year. Here, our scientists develop innovations for battery cell production under the highest production standards. To ensure that the end products also meet the high-quality requirements, it is necessary to test the finished battery cells under real conditions - this task may soon be taken over by robots. Because even if it is still difficult for many people to imagine intelligent machines taking over the tasks of skilled workers, this could result in a number of advantages.
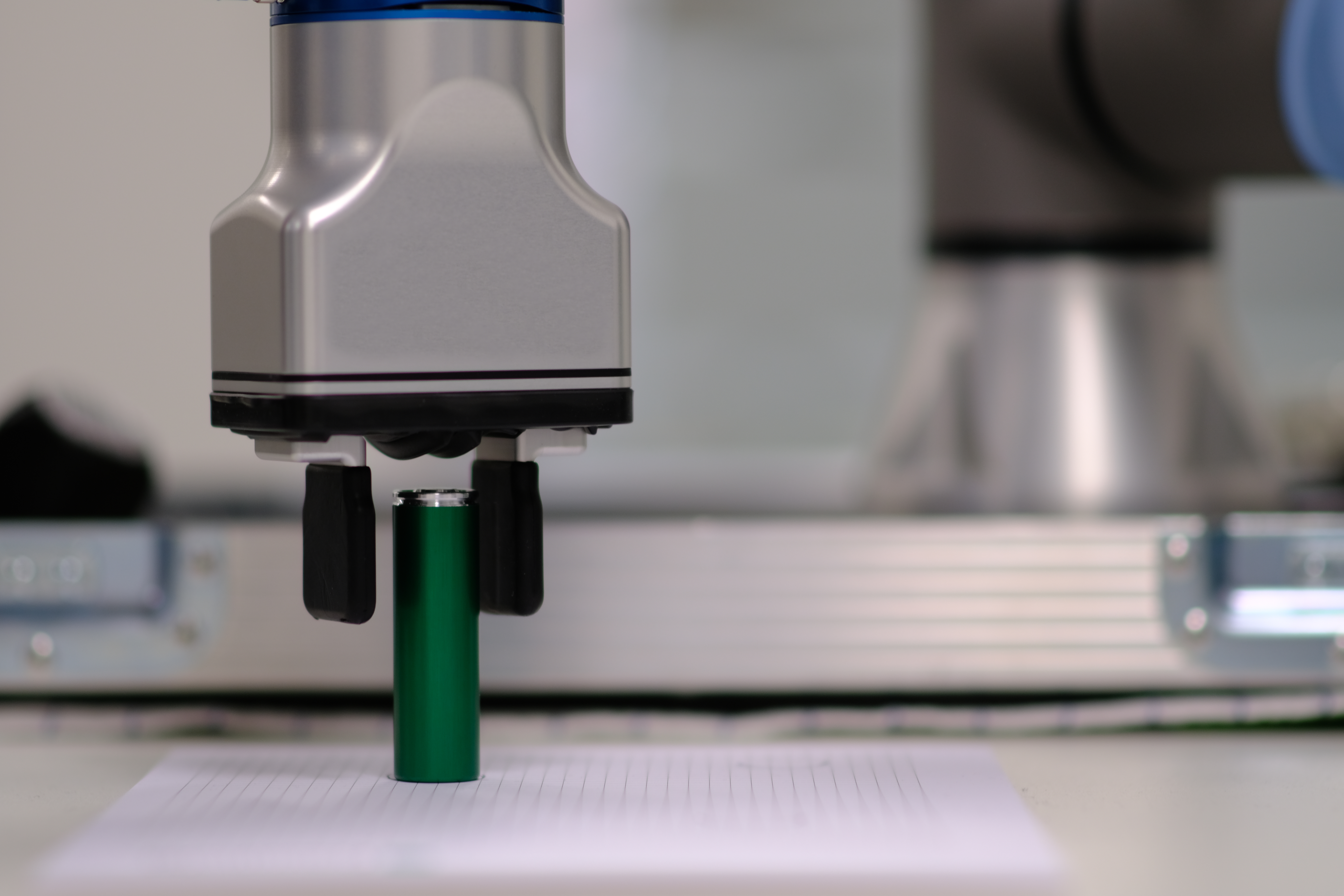
The "AutoBot" project, which started in January, is dedicated to testing battery cells and drawing conclusions from measurement data about production. Through collaboration between the Institute for Power Electronics and Electrical Drives ISEA at RWTH Aachen University and Fraunhofer FFB as project partners, an automated test station is being developed. With the help of an automated handling system, consistent test conditions are generated, and the battery cells are inventoried and examined.
In the project, a test station will be created at ISEA where investigations of different parameters, such as dimensions and weight, but also the behavior under load and long-term use can be carried out. In addition, a computer tomograph will be available to monitor the chemical processes within the cell and the behavior of the active materials and to enable detailed evaluation.
In order to ensure continuous throughput and consistent testing criteria, automation of the testing plays a major role. Therefore, a robotic arm is used at the testing station. This is designed to grip the delivered battery cells and check them for the various requirements in several runs. This not only promotes efficiency but also ensures ongoing comparability of the results.
"Quality monitoring pays off - especially for product quality and resource conservation" - Lukas Kokozinski, Production Technology
In addition to the development and set-up of the testing facility, the exchange of the data generated in the process is also an essential part of the "AutoBot" project, with a focus on direct data exchange between ISEA and cooperation partners. In this way, the collected information can be directly integrated into battery cell production. This offers a variety of advantages: Using the collected data can enable more efficient production and higher-quality results. This not only ensures better products but also reduces the number of potential rejects - a big plus in terms of sustainability.
In addition, the data not only benefits individual cooperation partners but also ensures that all participants have access to a wide range of information, for example on possible sources of defects. This exchange promotes sustainability-oriented and scalable battery cell production in Germany and Europe.
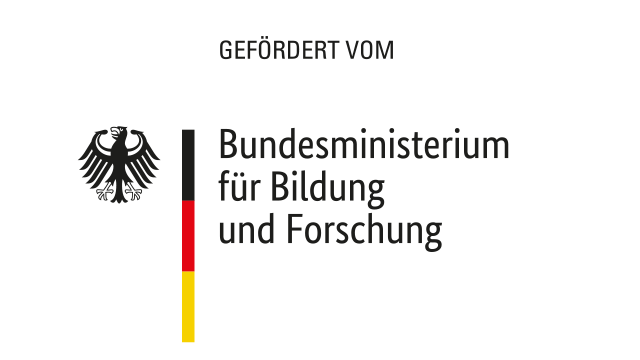

Last modified: